Recognizing the Essentials and Applications of Plastic Extrusion in Modern Production
In the world of modern manufacturing, the method of plastic extrusion plays an important function - plastic extrusion. This elaborate process, entailing the melting and shaping of plastic with specialized dies, is leveraged across various industries for the development of diverse products. From vehicle parts to customer products product packaging, the applications are vast, and the possibility for sustainability is just as excellent. Untangling the basics of this process reveals the true convenience and capacity of plastic extrusion.
The Basics of Plastic Extrusion Process
While it may show up complex, the principles of the plastic extrusion process are based on relatively straightforward principles. It is a production procedure in which plastic is thawed and after that shaped right into a continuous account via a die. The raw plastic product, commonly in the type of pellets, is fed into an extruder. Inside the extruder, the plastic goes through warm and stress, triggering it to thaw. The liquified plastic is then forced through a designed opening, understood as a die, to develop a long, constant item. The extruded item is cooled and after that reduced to the desired length. The plastic extrusion process is extensively used in numerous industries due to its cost-effectiveness, efficiency, and flexibility.
Different Sorts Of Plastic Extrusion Techniques
Building upon the basic understanding of the plastic extrusion process, it is required to check out the different methods entailed in this production technique. In comparison, sheet extrusion develops big, level sheets of plastic, which are generally more refined right into products such as food packaging, shower drapes, and vehicle components. Recognizing these techniques is crucial to using plastic extrusion efficiently in modern manufacturing.

The Function of Plastic Extrusion in the Automotive Sector
A frustrating majority of components in modern-day vehicles are products of the plastic extrusion procedure. This procedure has changed the automobile industry, transforming it into an extra reliable, economical, and adaptable production field. Plastic extrusion is mainly made use of in the manufacturing of various automobile components such as bumpers, grills, door panels, and control panel trim. The procedure offers an attire, regular output, enabling suppliers to generate high-volume get rid of excellent precision and minimal waste. The agility of the extruded plastic parts adds to the total decrease in vehicle weight, boosting gas effectiveness. The sturdiness and resistance of these parts to warmth, cold, and impact enhance the longevity of cars. Therefore, plastic extrusion plays a pivotal function in auto manufacturing.

Applications of Plastic Extrusion in Consumer Product Production
Beyond its considerable effect on the vehicle industry, plastic extrusion confirms similarly reliable in the world of customer goods manufacturing. This procedure is vital in creating a broad range of items, from food packaging to family devices, playthings, and also clinical tools. The convenience of plastic extrusion allows makers to design and create complex shapes and sizes with high accuracy and effectiveness. In addition, due to the recyclability of lots of plastics, squeezed out elements can be reprocessed, decreasing waste and cost. The versatility, versatility, and cost-effectiveness of plastic extrusion make it a favored option for several durable goods producers, adding considerably to the industry's growth and technology. Nonetheless, the ecological effects of this widespread use call for mindful factor to consider, a subject to be gone over further in the subsequent section.
Environmental Impact and Sustainability in Plastic Extrusion
The pervasive use of plastic extrusion in producing welcomes scrutiny of its ecological ramifications. As a process that often makes use of non-biodegradable materials, the environmental effect can be significant. Energy intake, waste manufacturing, and carbon discharges are all worries. Nonetheless, industry innovations are increasing sustainability. Reliable machinery decreases energy use, while waste administration systems recycle scrap plastic, reducing raw material needs. Furthermore, the development of eco-friendly plastics offers a more eco friendly choice. In spite of find these renovations, better innovation is required to reduce the environmental footprint of plastic extrusion. As culture leans in the direction of sustainability, makers have to adjust to remain feasible, stressing the relevance of constant study and advancement in this field.
Conclusion
In conclusion, plastic extrusion plays an essential duty in contemporary production, particularly in the automotive and customer goods fields. Recognizing the basics of this process is essential to enhancing its advantages and applications.
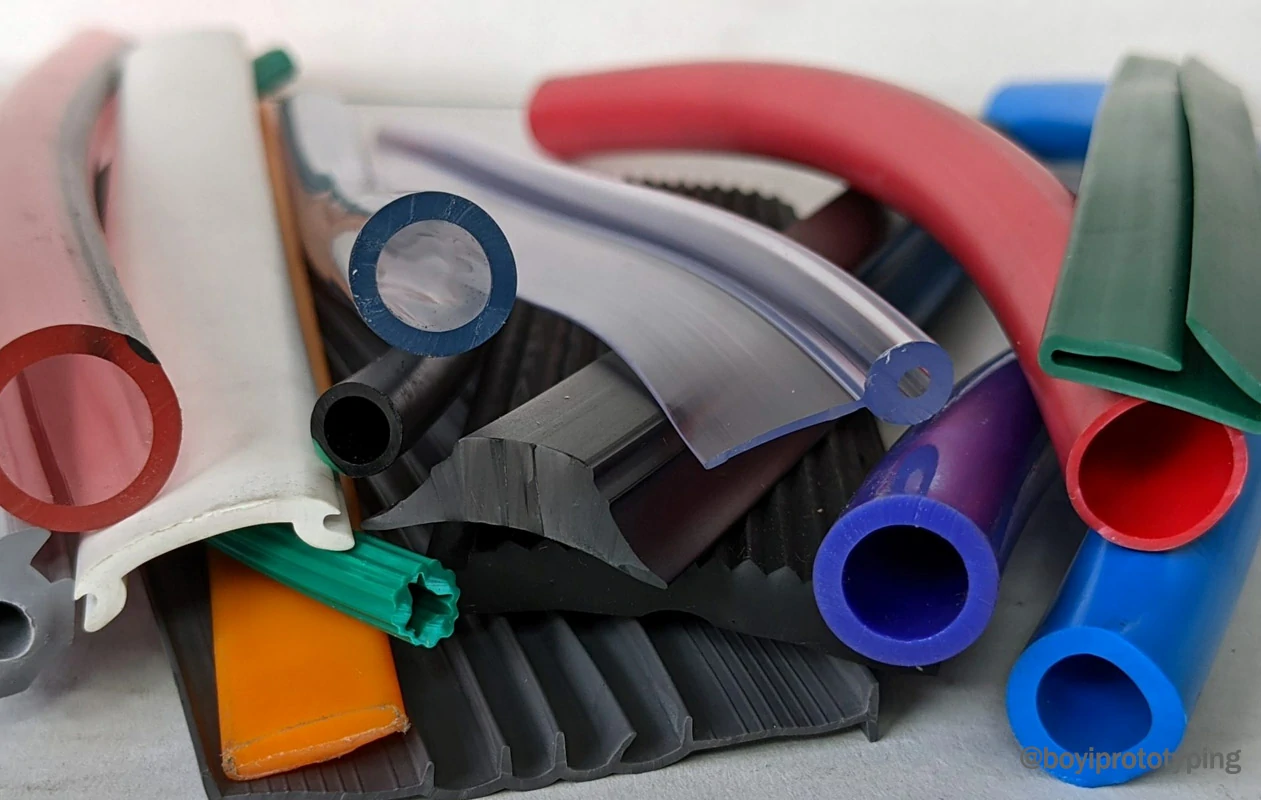
The plastic extrusion procedure is thoroughly made use of in numerous industries due to its cost-effectiveness, versatility, and efficiency.
Building upon the fundamental understanding of the plastic extrusion process, it is required to explore the different techniques involved in this manufacturing method. plastic extrusion. In contrast, sheet extrusion produces huge, flat sheets of plastic, which are normally additional processed into items such as food packaging, shower drapes, and automobile components.A frustrating majority click here for info of components in modern-day lorries are items of the plastic extrusion see page procedure